Welding is both an art and a science, demanding precision, patience and knowledge. Whether you're a hobbyist or a professional, mastering welding requires understanding the common mistakes that can occur and learning how to avoid them. To help, the Rapid Welding team have compiled some of the most frequent welding mistakes and tips on how to sidestep these pitfalls to ensure strong, reliable welds. Enjoy!
- Improper Preparation
Mistake: One of the most critical steps in welding is often the most overlooked – preparation. Failing to properly clean and prepare the surfaces to be welded can lead to weak welds, contamination and defects.
Solution: Always clean the welding surface thoroughly before starting. Remove any rust, paint, oil or dirt. Use a metal brush or grinder for the best results. Ensuring your workpiece is clean and properly prepared is the first step towards a strong and durable weld.
- Incorrect Welding Techniques
Mistake: Using the wrong welding technique can lead to numerous problems, including poor penetration, excessive spatter and uneven welds. This often happens when welders are not familiar with the specificities of the material or the welding process.
Solution: Invest time in learning and practicing different welding techniques. Understand the characteristics of the materials you are working with and adjust your technique accordingly. For instance, thinner materials require more delicate welding techniques to avoid warping or burning through.
- Inadequate Shielding Gas Coverage
Mistake: In gas metal arc welding (GMAW) and tungsten inert gas (TIG) welding, not using enough shielding gas or using the wrong type of gas can expose the weld pool to atmospheric gases, leading to porosity and contamination.
Solution: Ensure you're using the correct type and amount of shielding gas for your project. Regularly check your gas bottles, hoses and regulators for leaks. Adjust the gas flow rate according to the welding conditions, such as the type of material and the presence of drafts.
- Incorrect Welding Speed and Temperature
Mistake: Welding too quickly or too slowly or at an incorrect temperature, can compromise the strength and appearance of the weld. Fast welding may lead to inadequate penetration, while slow welding can cause excessive heat input, leading to warping and distortion.
Solution: Practice controlling your welding speed and pay attention to the weld pool's size and the metal's behaviour as you weld. Adjust your speed and temperature settings based on the material thickness and type.
- Using the Wrong Equipment or Settings
Mistake: Using inappropriate equipment or incorrect settings for the job can lead to poor-quality welds. This includes using the wrong type of electrode, incorrect voltage settings or unsuitable welding machine for the material.
Solution: Familiarise yourself with different welding machines and their settings. Choose the right electrode and adjust your machine's settings based on the material you're welding. Always refer to the manufacturer's recommendations and guidelines. And remember if you still have questions, get in touch with the Rapid Welding team. We are always happy to advise you.
- Neglecting Safety Practices
Mistake: Overlooking safety measures can lead to accidents, injuries and long-term health issues. Common safety oversights include not wearing appropriate protective gear or working in an unsafe environment.
Solution: Always wear the proper safety gear, including gloves, a helmet with the correct shade of lens and protective clothing. Ensure your workspace is well-ventilated and free from flammable materials. Safety should always be your top priority.
Always Be Prepared
Welding is a skill that requires constant learning and practice. By understanding and avoiding these common mistakes, you can improve the quality of your welds and ensure the safety and longevity of your projects. Remember, the key to becoming a proficient welder lies in patience, practice and a keen eye for detail.
For all your welding needs, from equipment to expert advice, visit the Rapid Welding website. You also always contact our friendly sales team on +44 (0) 23 92 214 214 or email webenquiries@rapidwelding.com. We look forward to speaking soon!
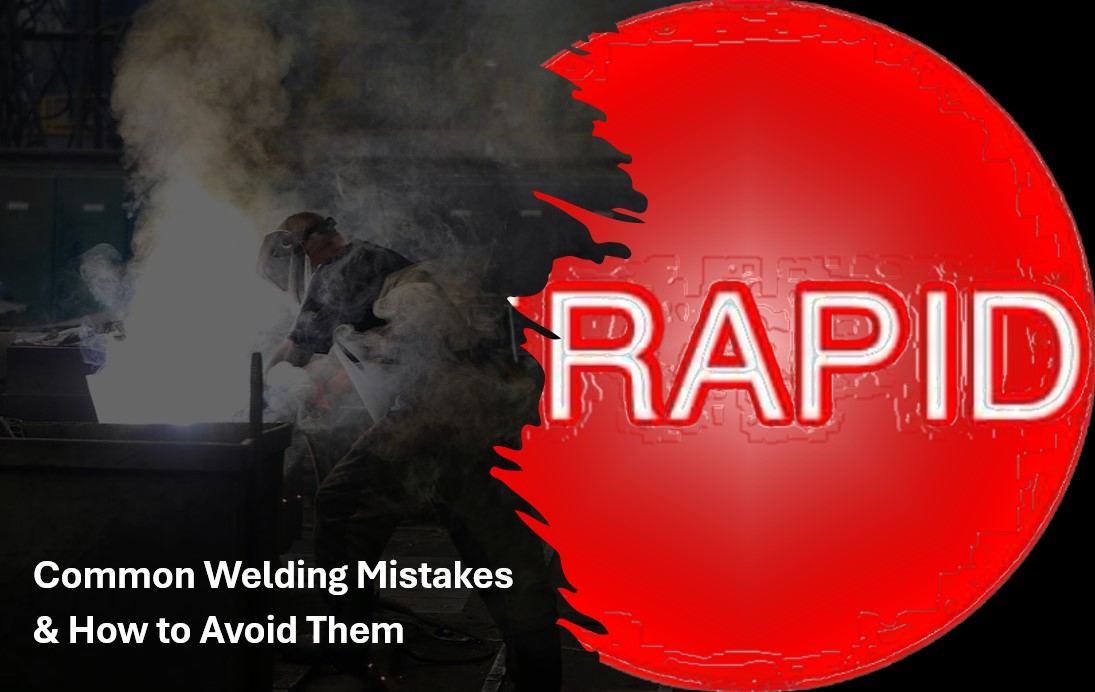
Leave a Comment